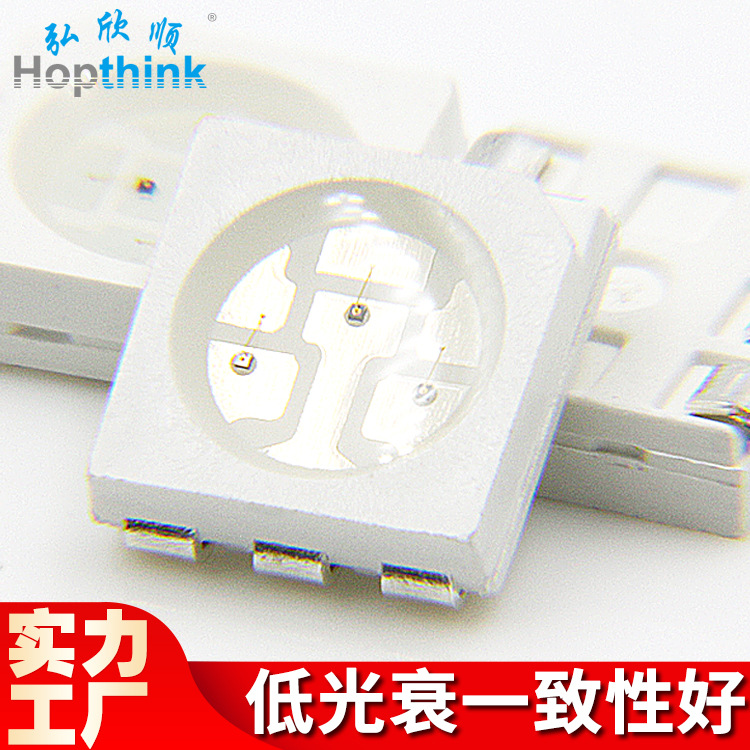
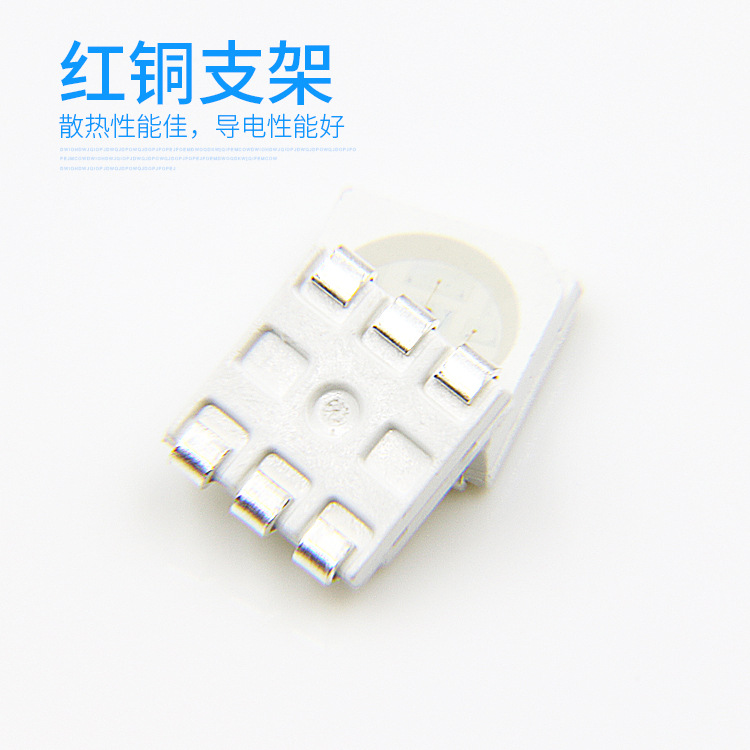
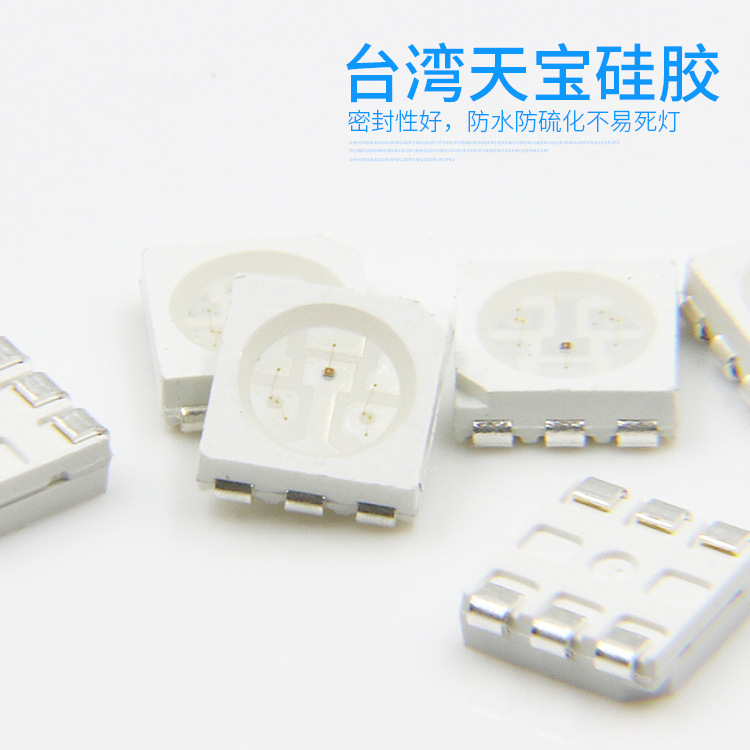
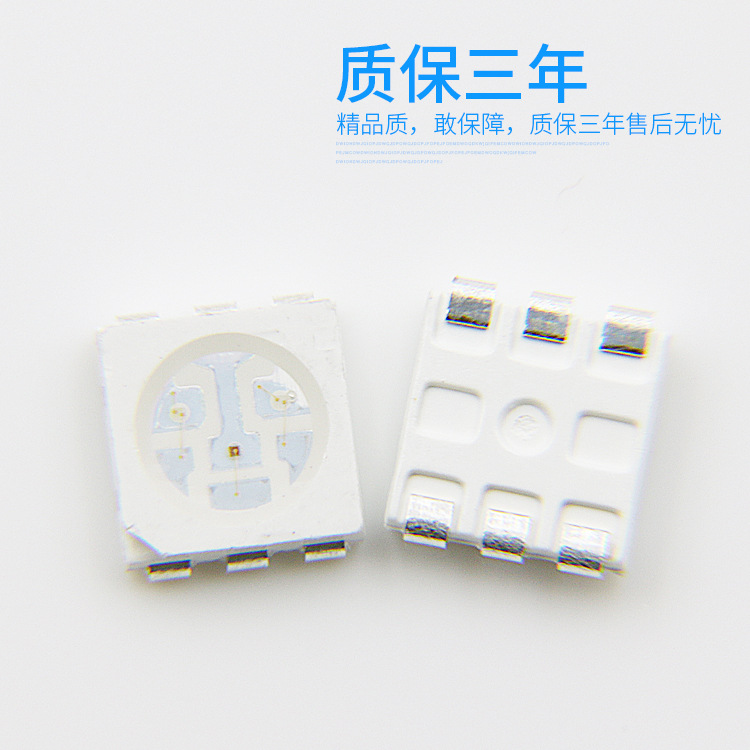
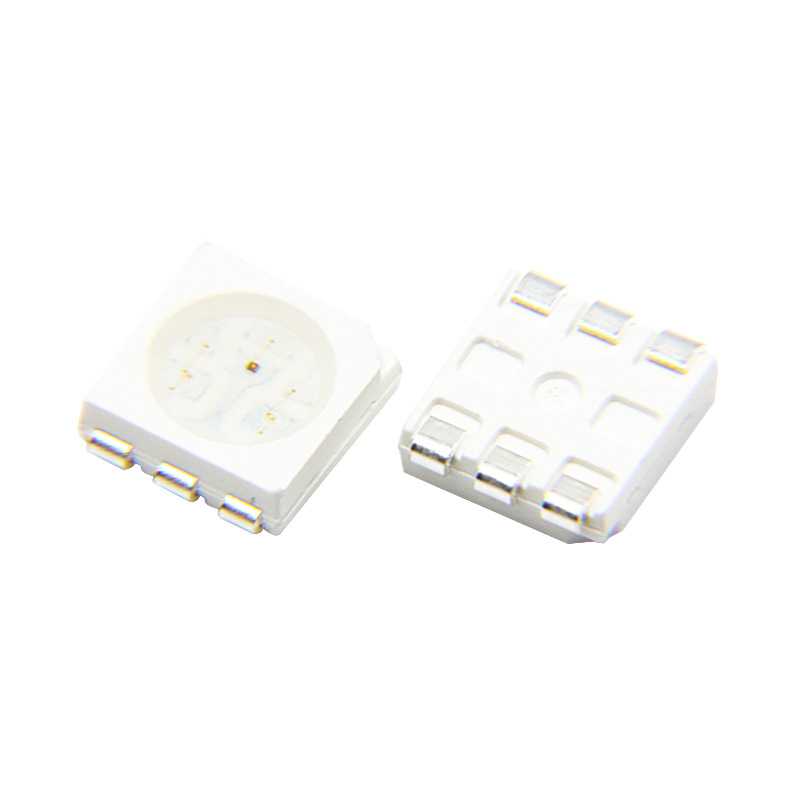
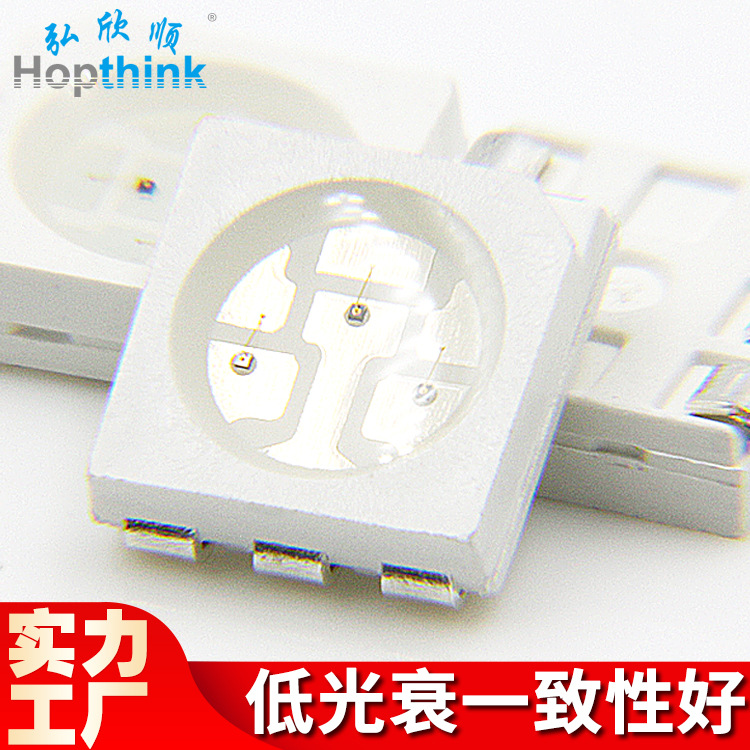
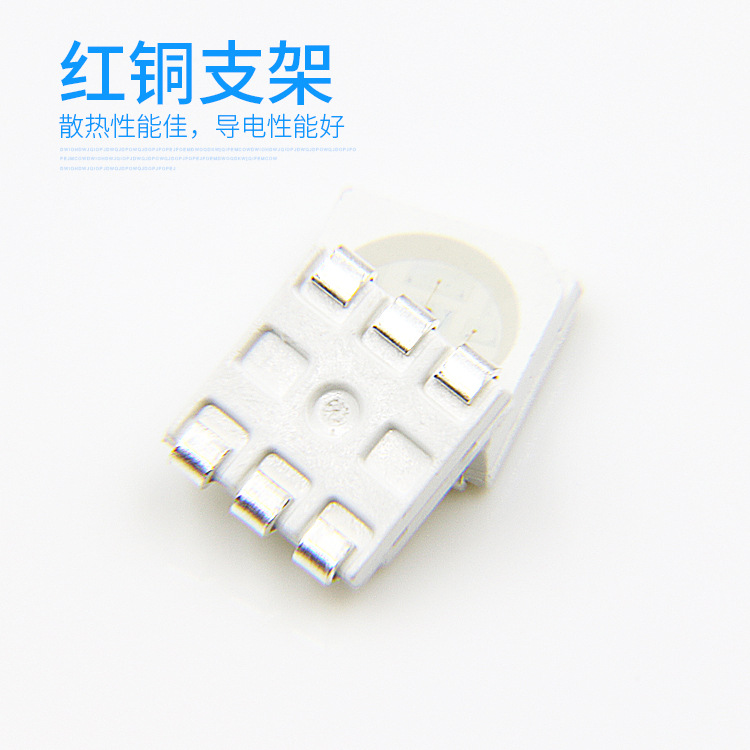
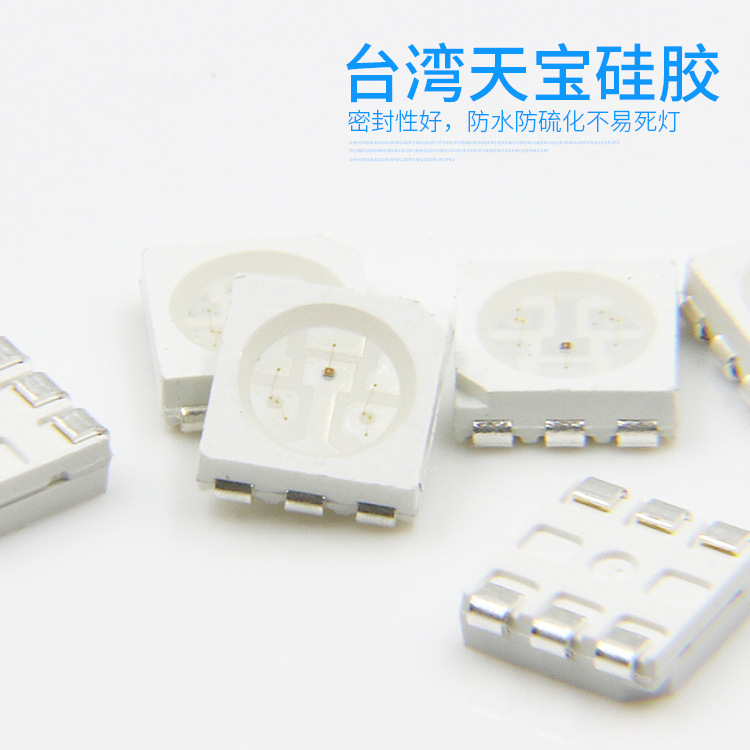
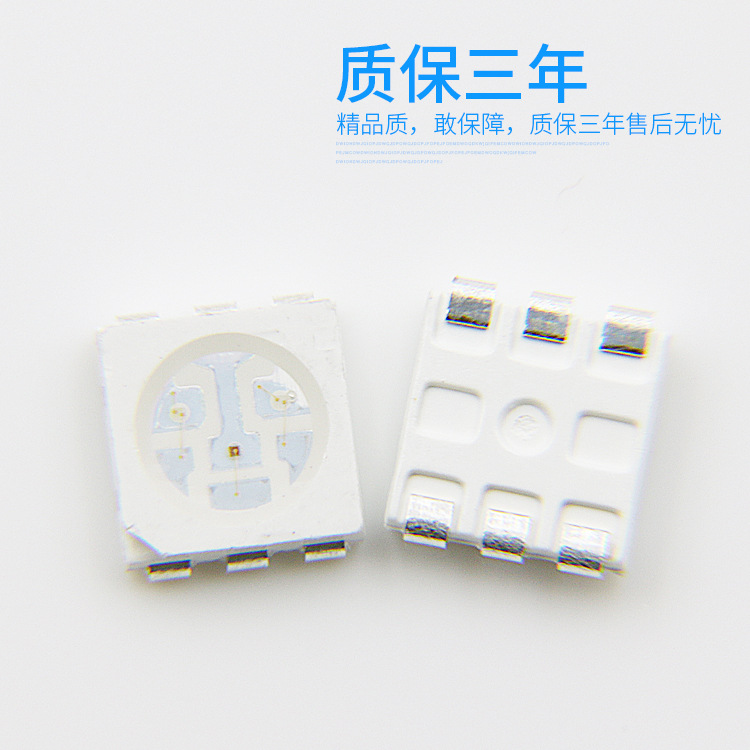
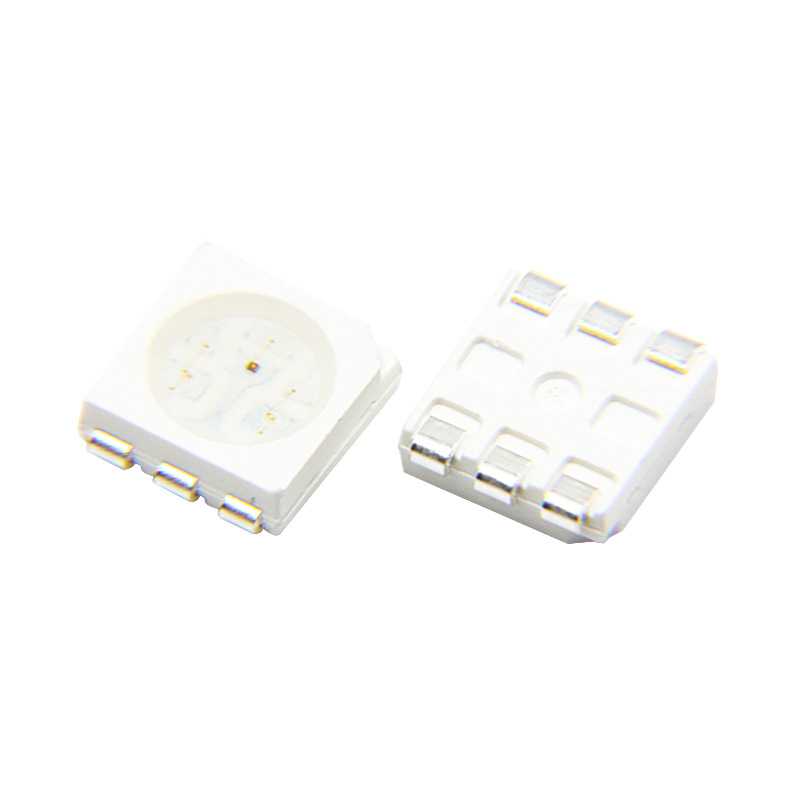
■ Instructions for use
1. Overcurrent protection
Customers must use resistance to protect, otherwise the voltage drift will cause a large change in current (breakdown phenomenon).
When the lamp bead is used, the current must be within the specified range to avoid excessive current resulting in bad.
Step 2 Store
2-1. Do not open the moisture-proof bag before preparing to use the product. Before opening the bag, check whether there is air leakage. After opening the bag, check whether the 20%RH area on the humidity label card changes from blue to pink. If air leakage or discoloration occurs, please contact the manufacturer or return to the manufacturer for high temperature dehumidification treatment (high temperature dehumidification environment: 120 degrees, 6H)
2-2. Before opening the package, LEDs should be stored at temperature below 30℃ and humidity below 70%RH.
2-3. After opening the package, under the condition that the temperature is below 30℃ and the humidity is below 60%RH, and the opening is controlled within 4H until the welding is completed.
2-4. If the hygroscopic material (silicon gel) has faded or the LEDs have exceeded the storage time, baking is required based on the following conditions: 60±5℃/ 24 hours.
3. Precautions for reflow soldering
3-1. Temperature curve of lead-free solder paste
3-2. Reflow not more than twice.
3-3. Do not add any pressure to the LEDs when heating during welding.
3-4. After welding, the normal return temperature is below 40℃ before the current can be passed.
4. Protective measures
Use appropriate tools to clamp from the side of the material, because the product uses silicone packaging to avoid crushing the colloid in the application process, damage the internal structure caused by bad. Leds are semiconductor sensitive devices, and electrostatic discharge (ESD) or pulsed current (EOS) may damage leds. Effective grounding of the machine and electrostatic protection during operation can effectively improve product quality. The chip LED lamp beads should be avoided in the production process and the lighting environment. Halogen. Acid. Alcohol. Base. Ketoxime volatile compounds, strong oxides. Plasticizer (also known as plasticizer, leading dioctyl phthalate DOP or dibutyl phthalate DBP,PVC materials contain a large number of plasticizers) and other corrosive substances contact.